Quality management to benefit our customers
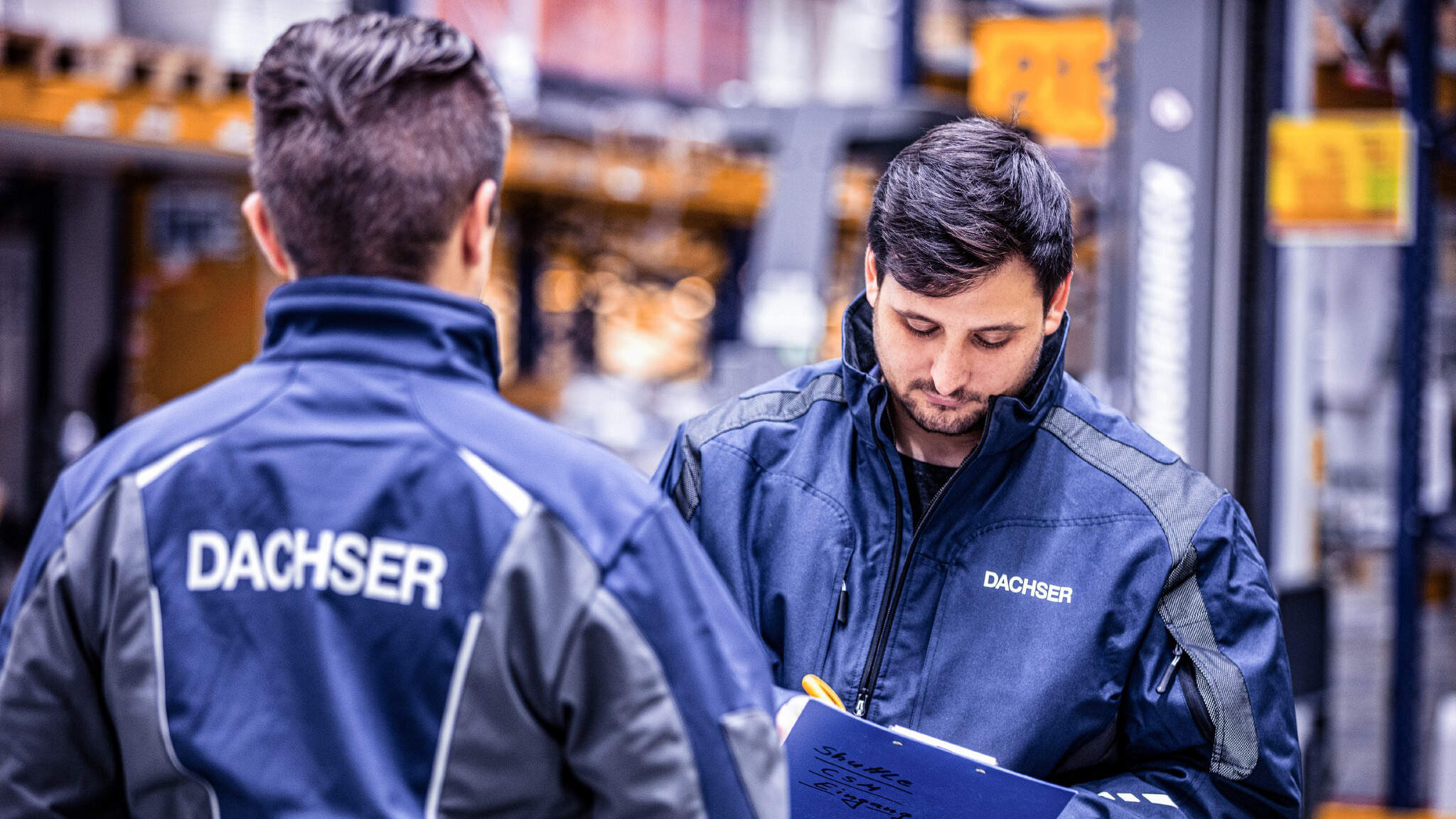
DACHSER’s certifications
- DIN EN ISO/IEC 27001:2017 (DACHSER IT)
- DIN EN ISO 9001:2015 (DACHSER Food Logistics & DACHSER Cargoplus Food)
- Certification in accordance with IFS Logistics (DACHSER Food Logistics & DACHSER Cargoplus Food)
- BIO certification (DE-ÖKO-003) in accordance with (EU) 2018/848 (DACHSER Food Logistics)
- QS meat and meat products as well as fruits, vegetables and potatoes (DACHSER Food Logistics & DACHSER Cargoplus Food)
- SQAS, Safety & Quality Assessment System (DACHSER Chem Logistics)
DACHSER’s awards
Air freight
- Lufthansa Quality Award Europe & Africa 2014
- Cargo Quality Award Germany (multiple winner)
- Global Partner since 2012
- Cargo Quality Award Europe & Africa 2014
- Cargo Quality Award 2015
- Planet Award of Excellence 2016
Satisfied clients are proof of our high quality standards
Almost 90 percent of our customers are highly satisfied with our logistics performance and would recommend us to others. This is according to a representative survey of 4,100 customers, which has been conducted every two years for more than 20 years. Customers are also asked to rate the quality of service requests, shipping services, security and customer service. The proactive supply chain event management tool ActiveReport also contributes to the high level of customer satisfaction.
Our quality management is based on three pillars
- The DACHSER network: The efficient logistics infrastructure of the global network and the intelligent IT enable a timely and efficient handling of a wide variety of logistical challenges
- Intelligent traffic management: As a learning organization, we adapt all new technological developments for the optimization of the supply chain in real time, and quickly transfer innovations into real-time operation, for you
- Excellent personnel: We consistently invest in the training and development of our employees in order to maintain a high level of logistics performance and quality in the long term
The quality management of DACHSER in detail
We owe our role as a leader in quality on the logistics market to our active and forward-thinking quality management. This includes integrated IT systems and a consistently transparent freight movement thanks to standardized processes. High-performance transshipment areas enable long-term quantity control: vacation seasons and public holidays are incorporated into the planning of the logistics chain from the onset. With evaluations several times per month, daily performance checks, and regular audits, we make the quality of our service transparent and quantifiable. Our standard logistics processes at every stage of the supply chain lead to a low loss ratio and increase your delivery reliability.
In order to ensure a consistently high level of logistics services, we rely on the following methods of quality assurance and control:
- Regular customer satisfaction surveys
- Consistent quality control through the analysis of key performance indicators (KPIs) along all logistics processes
- Active damage prevention with on-site measures
- Security during transport, with Europe-wide network control, IT-led processes and timely reporting in the event of deviations in the transport process via the supply chain event management tool ActiveReport
- Globally networked DACHSER IT systems and physical network locations
We attach the highest importance to the security of your goods. Our security measures include video surveillance of our buildings as well as high-quality equipment. Our permanent staff are highly trained in all core logistics processes, ensuring the flow of goods, both physically and digitally. Regular training for drivers and logistics operatives, established standards for loading and unloading, conscientious load securing, temperature monitoring, and hygiene practice also contribute to the protection of your freight.
Tried-and-tested load-securing devices such as stowage sacks, seals with their own ID as well as automated processes with consistent electronic interface documentation also ensure comprehensive protection along the supply chain. We verify loading quality as part of our regular checks. In order to avoid damage in transit, we use box trailers with double-deck capacity.