A solid footing worldwide
Homes without any wood-based products from Austrian manufacturer Kaindl/Kronospan are few and far between. Achieving such widespread distribution poses quite the logistical challenge.
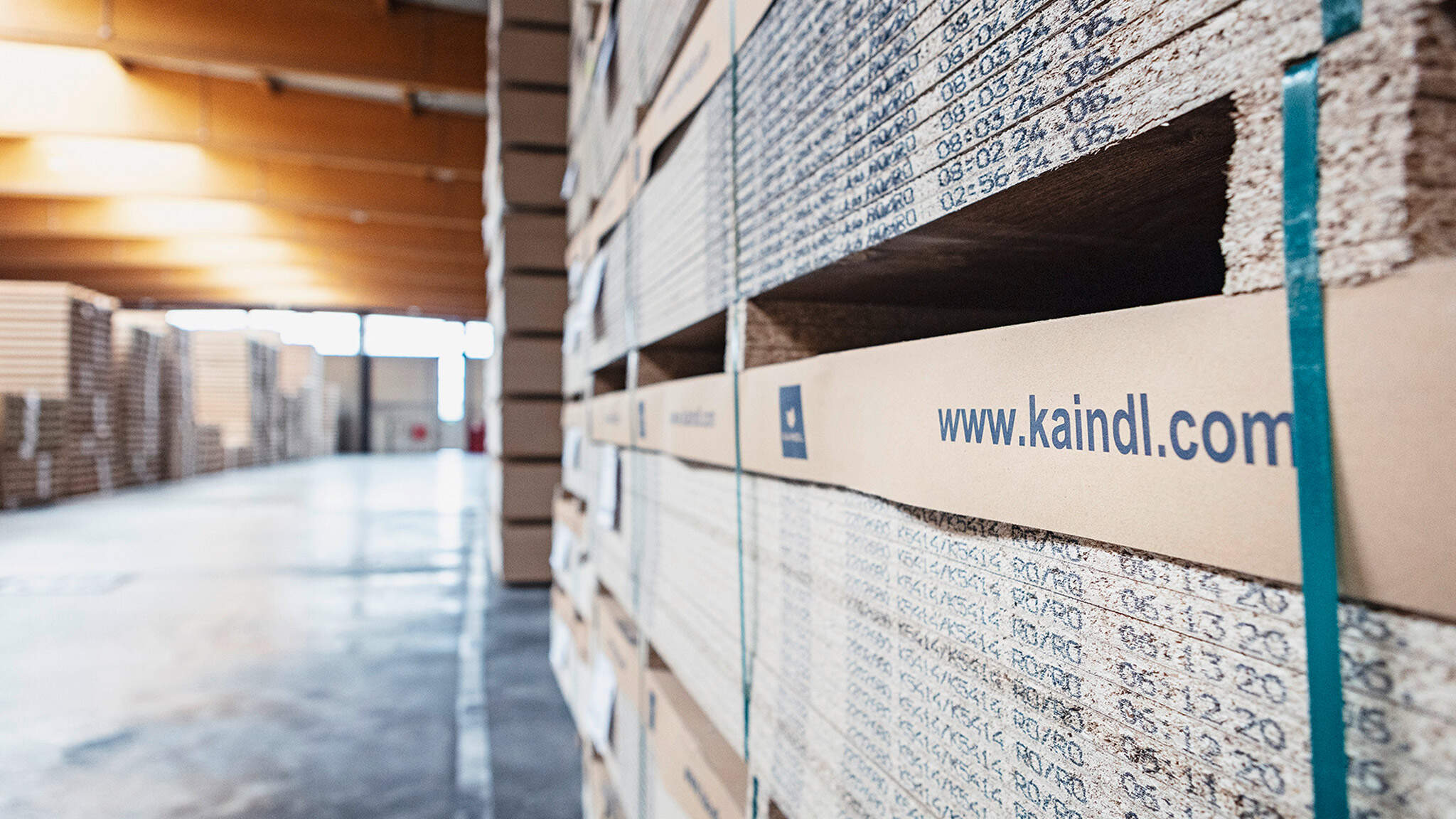
Salzburg-based family business Kaindl, which operates internationally under the name Kronospan, is the world’s leading manufacturer of wooden, laminate, and designer flooring as well as decorative panels and worktops. Thousands of full container loads packed with all kinds of wood-based products leave its plants in Austria every year, destined for retailers and manufacturers in locations as distant as the Far East and the Americas.
For ten years now, DACHSER has been the company’s logistics partner. When the containers are ready for shipment, DACHSER uses tractor trailers to transport them from Kaindl’s plants in and around Salzburg to the Container Terminal Salzburg (CTS). From there, the goods make their way to Hamburg or Bremerhaven by rail, where they are loaded onto container ships departing on main carriage routes to various ports around the world. Some go to Tokyo, Osaka, and Nagoya in Japan, others head to the ports of Taichung or Keelung in Taiwan, or to the port cities of Veracruz and Altamira in Mexico.
Reliability is everything
“We’re a major European shipper, so ensuring the reliability of our transports is a top priority,” says Volker Lenzing, Chief Corporate Logistics at Kronospan. Since the margins on the products are low, it’s essential that the supply chain runs smoothly, he explains. For that reason, the Group doesn’t leave anything to chance and is always looking into ways to optimize container loading and the packaging.
"Because we’re dealing with wood-based products, it’s crucial that we communicate with the teams in the US and at Kaindl in Austria."
DACHSER has standardized procedures in place for each destination, including fixed loading periods to avoid demurrage and detention costs for the containers. It also sets out fixed transit times and provides an advanced schedule for the week ahead, which calls for a smooth flow of information. To enable Kaindl to monitor its shipments at all times, DACHSER introduced a dedicated IT solution that lets the company view all the relevant data online, including the conditions and weekly changes.
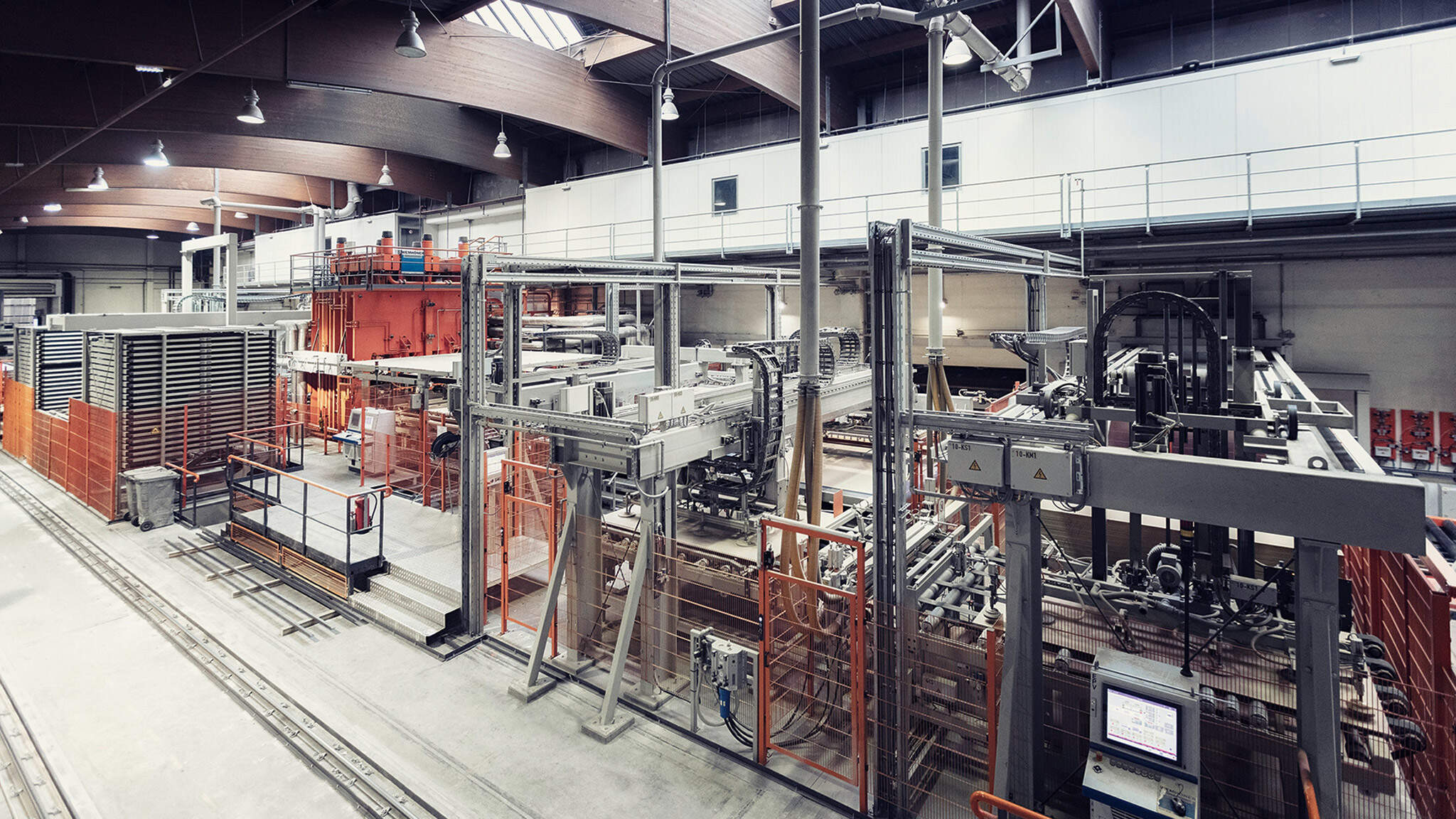
Rapid response required
Although Kaindl usually notifies DACHSER of the container quantities it needs weeks in advance, maximum flexibility is needed, explains Michael Rainer, Managing Director ASL East Europe and Austria. “As soon as we get the call from Kaindl, we have to reserve the appropriate number of containers at the CTS in Salzburg.” But there are times when DACHSER has to process orders with hardly any notice. “In some instances, we have to organize for CTS to provide 10 to 20 containers within 24 hours,” Rainer says, describing one of the challenges the logistics company faces. In those cases, acting quickly is essential, he adds, explaining that the availability of empty containers plays a major role. Managing that without creating additional costs for the customer is where the real skill comes in. The key is to use booked container spaces as efficiently and with as much advance planning as possible.
For Kaindl, the big plus is the scheduling reliability that DACHSER offers. “Kaindl needs assurance that its goods will be shipped on time,” Rainer says. And DACHSER provides just that: “Even though we’re handling such large shipments, we can proudly say that no deliveries have been delayed so far.” But DACHSER doesn’t just help with the company’s exports—it also imports materials for Kaindl, mainly aluminum oxide and paper, which the company uses to manufacture kitchen worktops and other products.
Entire machines shipped
While DACHSER’s work for Kaindl Salzburg primarily involves transporting full container loads for import and export, the logistics provider also deals with air freight and groupage shipments by sea for the Kronospan Group. When the company expanded its manufacturing capacity in Eastaboga, Alabama last year, DACHSER delivered more than 200 containers to the US, including some special oversize containers with production machinery for making particle board.
Other shipments, mostly individual deliveries of replacement parts, are shipped as less-than-container loads or as air freight. “Kaindl also uses our air freight service to send its latest products to the US to use as display stock,” Rainer says, explaining that Kaindl’s customers in the US and Canada receive sporadic shipments of new products directly to their showrooms. DACHSER and its partners in Canada also handle customs clearance when the goods arrive in the country. “Because we’re dealing with wood-based products, it’s crucial that we communicate with the teams in the US and at Kaindl in Austria,” Rainer says. “They have to make sure they provide us with the requisite documentation for the US authorities on time.”
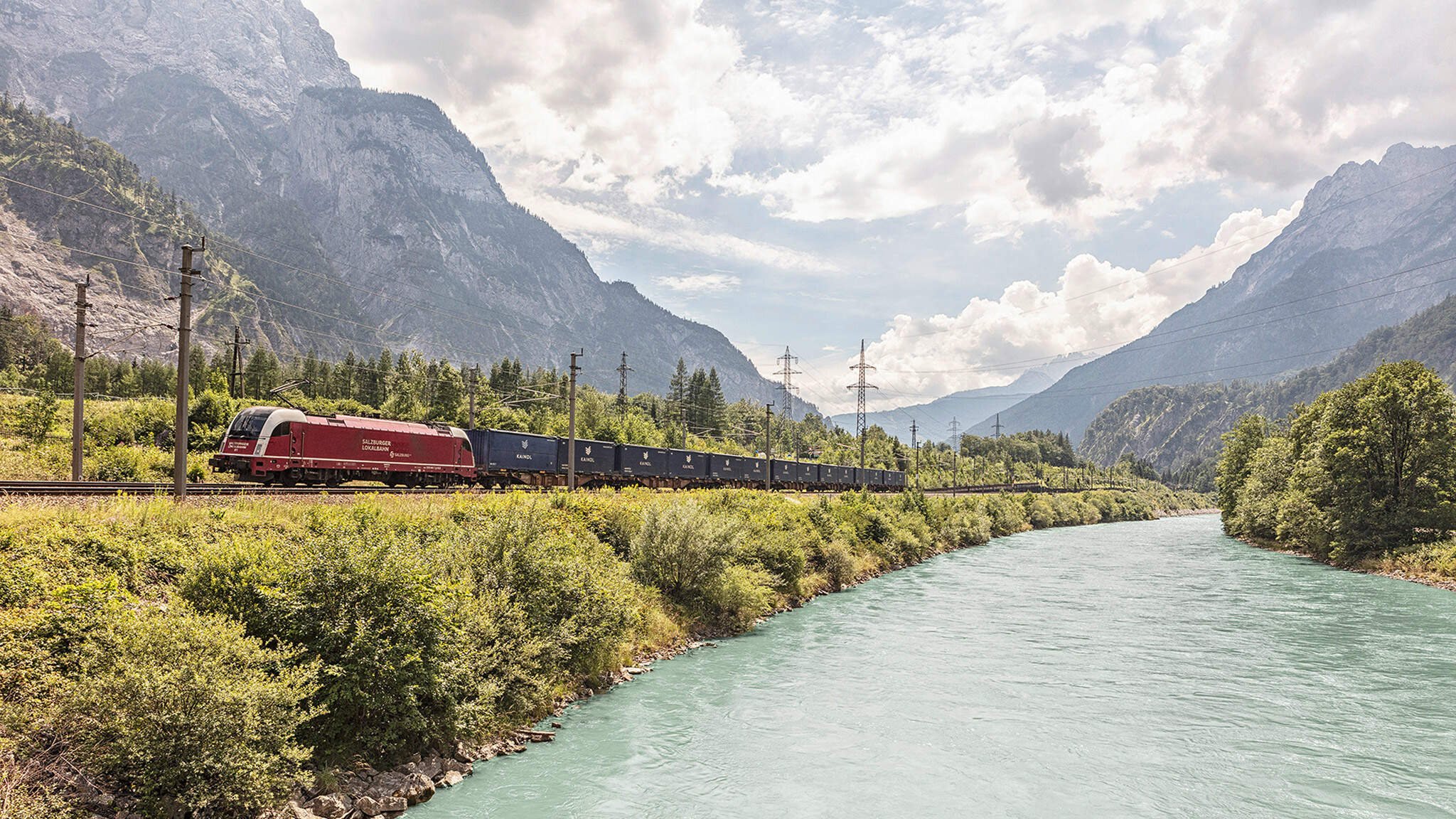
Acting fast to deliver PPE
DACHSER recently took on an additional assignment for Kaindl following the outbreak of the coronavirus pandemic. “During the first wave in the spring, we worked with DACHSER to import a large number of pallets containing personal protective equipment and masks from China for the medical sector,” Lenzing says. Kaindl then donated the urgently needed masks to various Salzburg hospitals.
“The key role we played in these transports was expediting the departures of the supplies by creating capacity with our own charter at a time when hardly any capacity was available on the free market. Because masks were already in such short supply, fast delivery was the top priority. The shipments were classed as emergency cargo and given precedence on our charter flights,” Rainer says.
“Our biggest problem turned out to be Austrian customs—at the time, they weren’t prepared for imports of these kind of goods,” Lenzing explains. The authorities couldn’t offer much help. “At that point, the customs rules were changing almost weekly due to the huge numbers of face masks being imported,” Rainer adds. “So DACHSER acted as an intermediary between the customs authorities and Kaindl to ensure that the latest requirements were being fulfilled and certificates, confirmations, and signatures were obtained on time.”
Despite all the red tape, DACHSER successfully transported the equipment from Shanghai Airport to Frankfurt, and from there organized a special delivery to Salzburg via Linz Airport for customs clearance.
Even though the mask shipment was a one-off, such a task would have been difficult to accomplish without the flexibility, rapid provision of capacity, and global network that DACHSER can offer. But ultimately, that’s what intelligent logistics is all about.